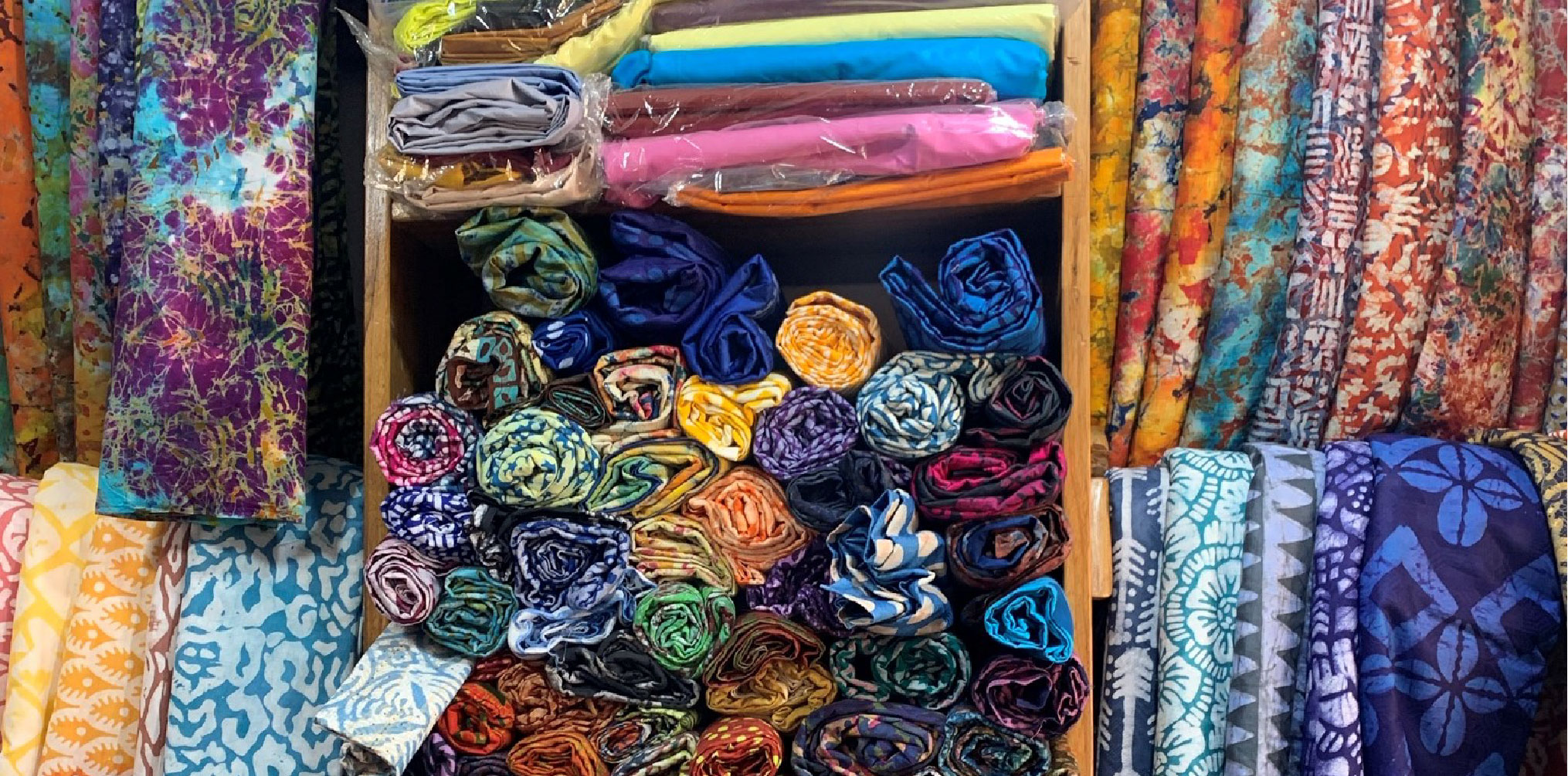
Research Grant Showcase: Interview with Johanna von Pezold
25.11.2021
Johanna von Pezold, the recipient of the CHAT 2021 Research Grant, talks to the CHAT team about her research background and recent trip to Ghana.
What is your research focus?
My background is in Chinese studies and I have always been interested in Sino-African relations. But rather than investment or infrastructure, I’m interested in the more personal, on-the-ground aspects of international politics. I want to write about people, and how people’s lives are changing through these types of connections.
For my own PhD, I am doing research on Chinese-made fashion products but also fabrics that are made in China and are now traded and consumed in Mozambique. You can find Chinese products everywhere, but they exist in very different contexts, and very different groups of people might present and sell these Chinese products in very different ways.
How has the pandemic affected your research?
I was initially afraid my topic would reach a dead end because of the pandemic travel restrictions, as especially China is very strict with immigration in and out. But not at all. These trade connections are so mature that people managed to continue trading through various platforms and channels. Certainly, there are disruptions to transport and shipping, and trading became more expensive, but the trading has kept going.
Trade moving online so quickly was a moment of realisation for me: the world is so globalised that it doesn’t break apart just because of a pandemic. In a way, it’s becoming even more intense, because now people can start a China business without ever going to China.
I realise the pandemic is a fascinating way to see the world getting tested. You can see what survives and what doesn’t and this tells you a lot about what the situation is like at the moment: how close relationships between countries and how tightly entangled different economies are. The pandemic is a magnifier of this. It tells us where the world is standing now.
Can you tell us something about fabrics that you found in your previous research in Mozambique?
Many different African countries have their own specific fabrics that are printed in different ways. In Mozambique, it’s the capulana. Capulana is a traditional cotton fabric that people use for dressing but also for other purposes. You can wrap a baby in it, use it as a picnic blanket, shelter yourself from the rain, and you can also tailor-make clothes out of it. By now, most of them are not only made but also designed in China, which I found really interesting. This for example is a new design which came out to the market last year: A COVID-19 capulana. I couldn’t resist getting one. Another thing I’m focusing on in my research is the brand craze and what authenticity means.
What is fascinating is that African prints have never been completely African, but they’ve also always been African. They have been produced in African countries too, but originally, the most highly valued, high-priced fabrics were always produced in the Netherlands or the UK. These companies later invested back into the African continent – they built their own factories there and they asked some local African companies to produce these fabrics. But the fabrics themselves always had this element of being foreign and coming from outside.
So that’s the mystery of African fabrics, how people make it their own even though it’s not produced in their own countries.
With CHAT’s Research Grant, you visited Akosombo Textiles Limited in Akosombo, Ghana. What was the factory like?
Akosombo Textiles, which is now called Akosombo Industry Commercial Limited (AICL), is about 100km away from the capital Accra, located next to a man-made lake and a hydroelectric dam, which was built in 1965 following Ghana’s independence as a project to promote their economy.
The location is perfect for a textile factory for a few reasons. First, many workers who were brought there to build the dam eventually settled there and sought employment. Because of the dam there was a source of electricity, and they also had access to water, which is needed not only for production but also for transportation. When they brought in raw cotton from northern Ghana, they could transport it over the lake, which was much faster than via the land route.
It’s also not too far from the Accra city centre, nor from the big ports in neighbouring Tema. Rather than in an industrial harbour complex, the factory site is situated in the middle of the forest, surrounded by mountains, which I found fascinating. The nearby town of Akosombo was built purposely for the dam workers, so it is very neat and tidy and nicely integrated into the environment.
In 2018-19, a new Ghanaian management took over from the Hong Kong management, who had been operating the factory since the 1960s. The partly state-owned company is now employing about 700 workers. For my research trip, I got to see all the steps of the production process and met with the director and managers who shared with me their daily tasks and challenges. It was also wonderful to see all the machines in action and the samples of all the fabrics ever printed.
Can you tell us more about this moment from your site visit?
What you see here are rotary screens. Most of the simple or ‘fancy’ print fabrics are made with such screens. These rollers are made of metal and can be engraved with lasers to create specific patterns. Each roller is one colour. The dye is contained inside the roller and applied onto the fabric through the engraved holes or lines. Therefore, you need several of these rollers to print one pattern. Each roller is very thin but also strong enough to stand by itself.
Everything is done on-site, from engraving to printing. The rollers can be stored or recycled if new designs reuse certain elements of an existing pattern or are kept for reprinting if clients expand on their previous orders. I have been to textile factories before, the one in Mozambique for example, but this the first time I’ve seen the rollers displayed this way.
Can you tell us more about this method of rotary screen printing?
There are different ways of simple industrial printing. The first is dipping the roller into the paint, or applying the paint onto the roller, before rolling it over the fabric. The more advanced method is using rotary screens with holes in them where the ink gets pushed through. Compared to roller printing, rotary screen printing is easier because it can be done continuously. You simply insert the colour and keep on rolling and printing, often yielding sharper and more precise prints.
Can you share a bit more about traditional African wax print fabrics production, then and now?
In wax printing, wax is first applied to the fabric. Then the fabric is fed through a machine which crumples it, and in the process some wax comes off in an intentionally irregular pattern. Afterwards, the fabric is dyed, and where the wax remains on the fabric, the colour will not go through. Then, you wash the wax off and you end up with the iconic ‘crackle’ effect.
With this method, you will never get the exact same metre or yard of fabric. This is a unique selling point for companies or brands like Vlisco or ABC, Akosombo’s premium line, which still produce wax print fabrics with actual wax.
For most of the fabrics nowadays, wax is no longer involved. Most Ghanaians I talked to actually refer to them as simply print cloth, or African prints. Often the edges of the fabric will be printed with the words ‘wax-printed’, but that merely refers to the name of the category of fabrics in general, rather than the printing technique itself.
Does Ghana have its own national textile?
Yes, Ghana has the kente. It is a woven fabric, and it is one of the few pre-colonial fabrics that still exist on the continent. Ghanaians are, rightly, very proud of this. Local kings and chiefs will always wear it for important occasions.
Kente strips are traditionally woven by hand, and they can be sewn together to make a larger fabric to be used as blankets or to be made into clothes. They are quite expensive as they are handwoven. Even though some are made in China nowadays, the original ones are still made in certain Ghanaian villages.
There are also printed fabrics that imitate kente patterns which are very popular among people who will wear them for parties and daily wear. These fabrics are way cheaper than the actual woven kente.
Akosombo and the other fabric factories in Ghana also do custom-made orders. If a family, company or ministry wants to have their own fabric for a certain occasion, they will engage a factory for custom-made work. These designs very often will not be found in the markets, as they are made for the clients specifically. One fabric that I did manage to find in the market was created for the 50th anniversary of Ghana’s independence, also made by Akosombo. Here you can see these Adinkra symbols, a sort of Ghanaian hieroglyph. Each of them has its own meaning and its own name. And for this design, they are applied on top of the kente pattern.
The only other place I was able buy these custom-made fabrics was at the University of Ghana. Each of the halls, and even each department, has their own traditional cloth which you can buy at the visitor shop. Students and teachers will usually have clothes tailormade from it, which they will wear for special occasions or celebrations at the hall or department.
Are young people wearing these fabrics?
Absolutely. At the universities, or if you go out to pubs and bars, you will see people wearing very trendy and cool outfits with these prints. Even people who work in offices or banks will wear shirts or skirts made of these print fabrics. There used to be a government initiative of National Friday Wear, where people will wear things made of Ghanaian-made print fabrics every Friday. I’m not sure if it’s still an official rule though.
Can you tell me more about the markets you visited?
One of the markets I went to was the Kejetia Market in Kumasi. It used to be an open-air market and was the biggest market in West Africa. Main visitors would be wholesalers, but locals can also do their normal grocery shopping there.
They have just about everything. All sorts of household things, and many many things from China. I’ve been to Yiwu in Zhejiang province before, which is the main trading hub for small commodities – keychains, socks, stationery etc. I actually recognised some of these things from that market, certain pieces of jewellery, or certain designs of souvenirs. I could tell, this comes from Yiwu. This proves again that many of the things sold all over the world just come from China.
But they also sell very ‘Ghanaian’ things, for example glass beads on strings, which women usually wear around their hips. They also have these handmade charms made of brass – many of which are made in China, but also ones that are made by artisans in Ghana. You can imagine the impressive sight of stalls of beads and beads and beads. It’s just beautiful.
Were there any unexpected linkages to Hong Kong?
Actually, I realised that the first Chinese communities in Ghana were Hong Kong-Chinese. Prior to the more recent influx of immigrants from the mainland, there had been more Hong Kong-Chinese living in Ghana than mainland Chinese.
Aside from Akosombo, there used to be other textile companies founded by Hong Kong investors which have since closed down because of difficulties in managing operating cost. Many of these Hong Kong textile workers then stayed in Ghana, and usually opened restaurants. You can have great dim sum in Accra!
What was the most memorable thing for you in this research trip?
The markets. They were so overwhelming, but strangely I also found that they put me at ease. I may not know where in the market I will find myself or where the exits are, but people are kind and helpful, so I knew I will be ok. It was overall a very pleasant experience where I could just throw myself into the hustle and bustle of market life.
Visiting the AICL factory was another highlight, which was a thing you wouldn’t do as a tourist at all. I really appreciated how friendly and welcoming the management was and how much time they took to show me around and make sure I can ask all the questions I want and see all the things I want. I’m very grateful to them.
I would still love to talk to some of the Hong Kong textile workers who used to stay at the factory in Ghana. They are probably all quite old now!
Find out more about her research here.
All images courtesy of Johanna von Pezold.